Suomen suurin metalli-3D-tuloste testattiin painelaitestandardin EN 13445-3 mukaisesti. Testitulokset esiteltiin kansainväliselle yleisölle marraskuussa Formnext-messuilla Frankfurtissa.
ANDRITZ Savonlinna Works Oy:n ja FAME-ekosysteemin yhteistyössä valmistama paineastia kesti LUT-yliopiston toteuttamat rikkomattomat ja rikkovat testit odotuksia paremmin. Kokeissa painetta lisättiin niin kauan, että kappale alkoi murtua. Tämä tapahtui 111 baarin paineessa.
”Tämä säiliö suunniteltiin 10 baarin käyttöpaineelle, mikä sisältää varmuuskertoimet. Alustava laskenta näytti, että murtuminen tapahtuisi noin 90 baarissa eli todellinen kestävyys ylitti reilusti odotukset. Täytyy huomioida, että oikeissa tuotantokappaleissa paineastian koeponnistus tehdään yleensä vain noin 1,5-kertaiselle käyttöpaineelle eli tässä tapauksessa koepaine olisi ollut vain 15 baaria”, sanoo lisäävän valmistuksen päällikkö Santeri Varis, ANDRITZ Savonlinna Works Oy:stä.
”Ennalta oli tiedossa, että pienessä mittakaavassa käytetyn menetelmän laatu on hyvä, mutta näin isosta koosta ei ollut kokemuksia. Olin yllättynyt noinkin korkeasta tuloksesta ja se kyllä vahvisti uskoa WAAMin hyvään laatuun”, hän jatkaa.
Noin 300-kiloinen paineastia on valmistettu ANDRITZ Savonlinna Works Oy:n 3D-tulostuslaitteistolla, jonka toimintaperiaatteena on suorakerrostus energianlähteenä valokaari (DED-Arc). Puhekielessä menetelmä tunnetaan WAAM-lyhenteellä (Wire Arc Additive Manufacturing). Haponkestävästä ruostumattomasta teräksestä (316 L) valmistetun noin 300-kiloisen paineastian halkaisija on 900 mm ja korkeus 1600 mm. Sen suunnitteluvaiheessa on ollut mukana myös Elomatic.
Pieni murtuma jalan viereen
Paineastiaa on testattu monin tavoin. Ensin sille tehtiin rikkomaton aineenkoetus (NDT) tunkeumanesteellä. LUT-yliopiston kokeissa testattiin sen materiaalista ja geometriasta määräytyvää suorituskykyä. Valmista kappaletta verrattiin muun muassa CAD-malliin, jota se vastasi parhaimmillaan keskimäärin kahden millimetrin tarkkuudella. Tämä on erittäin hyvä tulos, joka käytännössä selittyy tulostetun hitsin leveydellä.
Painekokeessa astiaan pumpattiin vettä ja seurattiin, mitä muutoksia se aiheuttaa astian leveimmän kohdan halkaisijaan. Painetta nostettiin aluksi asteittain ja lopuksi maksimiin.
”Alle 66 baarissa ei astiassa ollut vielä havaittavissa mittavia muutoksia. Muoto alkoi antaa periksi 80 baarin jälkeen. Jatkoimme testiä niin kauan, että astiasta vuosi vettä ulos 111 baarissa. Astian jalan viereen tuli siinä vaiheessa pieni halkeama. Siinä vaiheessa halkaisija oli laajentunut seitsemän prosenttia. Tulos on erittäin hyvä tämänkaltaiselle kappaleelle, joka on suunniteltu kestämään huomattavasti pienempää painetta”, sanoo tutkija Kalle Lipiäinen LUT-yliopistosta.
Halkeama hitsattiin kuntoon ja seuraavassakin testissä tuli murtuma juuri jalan kohdalle. Tämä kertoi siitä, että jalan alue oli rakenteellinen heikko kohta, eikä ensimmäinen hajoaminen johtunut esimerkiksi valmistusvirheestä.
WAAMin käytöstä suurissa kappaleissa on nyt syntynyt tietoa, jota ei aiemmin ole ollut saatavilla. FAME-ekosysteemi jakaakin tietoa yrityksille ja LUT julkaisee aiheesta tieteellisiä artikkeleja.
”Opimme testausprosessista paljon. Olisi hienoa, jos mahdollisuuksia toteuttaa suurten 3D-tulostettujen kappaleiden sekä hybridirakenteiden testejä olisi enemmän”, Lipiäinen sanoo.
Standardeja vaille valmista
”Testitulokset osoittavat epäilijöille, että 3D-tulostamalla voidaan tehdä laadukkaita kappaleita, kun tiedetään mitä tehdään ja ymmärretään suunnittelu- sekä valmistusprosessi. Nyt on vain kyse yritysten kyvystä adaptoida uusi teknologia osaksi omia valmistusprosesseja, sillä muuten on vaarana, että jää kilpailijoista jälkeen”, ekosysteemijohtaja Eetu Holstein DIMECC Oy:stä sanoo.
Suomessa monilla metalliteollisuuden yrityksillä olisi periaatteessa jo nyt kaikki edellytykset valmistaa omia 3D-tulostettuja painelaitteita sekä muita tuotteita, sillä WAAMiin tarvittava tulostuslaitteisto koostuu käytännössä robottihitsaussolusta ja robottihitsausvirtalähteestä, josta löytyy WAAM-prosessiin sopiva ohjelma.
3D-tulostettu paineastia ei kuitenkaan heti ilmesty markkinoille. Siihen on syynä standardisointi. Paineastioiden pitää täyttää painelaitedirektiivit ja EN-standardisointi on siinä vaiheessa, että työryhmä on perustettu. Tämä tarkoittaa, että muutaman vuoden päästä suunnittelulle ja tuotannolle voi olla olemassa standardit. Sitä odotellessa voidaan hioa prosessia ja testausta.
Paineastian tulostuksessa valokaariaika oli noin 100 tuntia, mutta todellinen tuotantoaika oli jäähdytyksineen, tarkastuksineen ja mittauksineen sekä opetteluineen noin 300 tuntia. Paineastiaan kului yli kolme kilometriä hitsipalkoa. Parhaimmillaan tulostusnopeus oli kolmen kilogramman tuntivauhtia.
Suomalaisen taidonnäytteen testaus on herättänyt kansainvälistä kiinnostusta, joten paineastiaa ja tuloksia esiteltiin Frankfurtissa lisäävän valmistuksen päätapahtumassa Formnext-messuilla.
”Meillä on Suomessa valtavan hyvä osaaminen 3D-tulosteiden suunnittelusta, valmistuksesta sekä testaamisesta. Pystymme erottautumaan maailmalla erityisesti vaativien tulosteiden osaajana, mikä tarkoittaa vaativia designeja ja käyttökohteita sekä kykyä tulostaa harvinaisempia materiaaleja. Yritämme tätä viestiä viedä ihmisten tietoisuuteen niin Suomessa kuin ulkomaillakin”, Eetu Holstein sanoo.
Paineastia ja testitulokset olivat esillä Formnextin pohjoismaisessa paviljongissa.
DIMECC Oy, Eetu Holstein, ekosysteemijohtaja
puh. +358 40 840 8660
eetu.holstein@dimecc.com
ANDRITZ Savonlinna Works Oy, Santeri Varis, lisäävän valmistuksen päällikkö
puh. + 358 40 860 6037
santeri.varis@andritz.com
LUT-yliopisto, Kalle Lipiäinen, tutkija
kalle.lipiainen@lut.fi
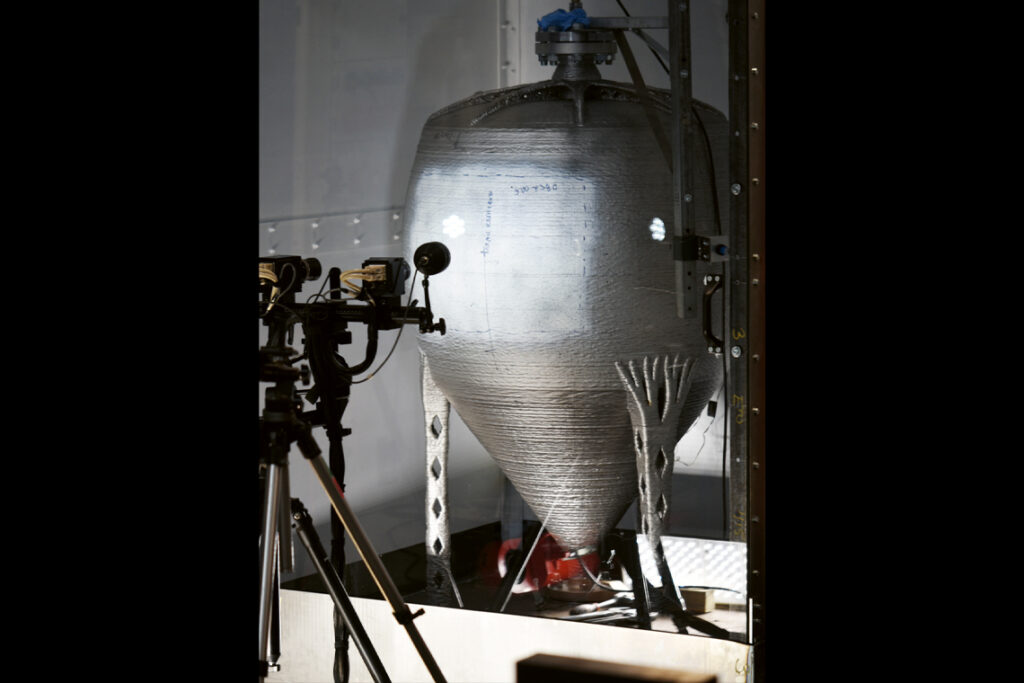