Tuotannon ja kunnossapidon osaaja Konecranes Machine Tool Service teknologiakumppaninaan Process Genius Oy ovat yhdistäneet osaamisensa asiakkaita palvelevaksi voimaksi. Uudessa 3D Digital Twin -pioneerisovelluksessa tuotannon ja kunnossapidon tunnusluvut ovat saatavissa samasta näkymästä ensimmäisten joukossa maailmassa.
Konecranes Smart Factory on fyysisestä tehtaasta tehty tarkka kolmiulotteinen digitaalinen kopio ja mallinnus (Digital Twin), jolla tehtaan reaaliaikaisia toimintoja ja prosesseja voidaan tarkastella selaimelta tai mobiililaitteelta. Smart Factory kerää alustaan tärkeää dataa eri ohjelmisto-, laite- ja anturirajapinnoista ja välittää tilannekuvan, mikä on saatavilla 24/7 tehtaan tuotannosta ja kunnossapidosta. Visuaalisesta mallista käyttäjä saa yhdellä silmäyksellä keskeisen tiedon tuotannon ja kunnossapidon tilanteesta. Smart Factory -älytehdasratkaisu tehostaa monin tavoin tietojen vaihtoa niin oman henkilöstön kuin asiakkaiden, palvelutoimittajien ja kumppaneiden kesken.
Miten määritellään Smart Factory?
Smart Factory tarkoittaa tuotannon digitalisointia yhä edistyneemmillä teknologioilla:
– teollisuuden esineiden internet (IIOT)
– lisätty todellisuus (AR, Augmented Reality)
– ohjelmistorobotiikka (RPA)
– lisäävä valmistus (3D)
– älytehdasratkaisut (digitaaliset kaksoset)
Päivittäisjohtamiseen tarvitaan mahdollisimman reaaliaikaista tietoa
”Olen seurannut työstökonemaailmaa lähes 25 vuotta, ja näkyvissä on selkeä muutos siinä mitä asiakkaat, yrityksen kokoon katsomatta, haluavat palveluntoimittajilta. Viime vuosina on noussut esille toistuvasti kysymyksiä, joissa on tiedusteltu: Kuinka voitaisiin visualisoida tuotantoa? tai Kuinka digitalisaatio näkyy Konecranesilla?”, kertoo Konecranesin työstökonehuollon Service delivery and development Manager, Jari Tuominen.
”Kunnossapito ei ole enää sitä, että kerran vuodessa huolletaan koneet ja väliajat korjaillaan. Suomessa on koneita monessa ikäluokassa ja niiden statusta halutaan seurata paikasta riippumatta. Päivittäisjohtamiseen tarvitaan mahdollisimman reaaliaikaista tietoa oman pajansa pulssista.”
”Konepajojen on kehityttävä, kun ohjelmistot ja koneet kehittyvät. Laitteet tuottavat paljon dataa, ja datalähteitä voi olla useita samassa tehtaassa. Selvitimme projektin alkuvaiheilla asiakkailtamme, onko heillä minkälaisia järjestelmiä kaiken tämän datan hyödyntämiseksi ja miten he pystyvät käyttämään dataa liiketoiminnassaan”, Jari Tuominen kertoo.
”Selvisi, ettei kenelläkään ollut käytössä vain yhtä systeemiä, vaan kaikki joutuvat käyttämään lukuisia eri järjestelmiä kerätäkseen tiedon siitä, mitä tapahtuu omassa laitoksessa. Lisäksi tehtaan eri tasoilla oli paljon eriäviä tarpeita. Myös erilaisia Digital Twinejä oli jo käytössä sekä erilaisia portaaleita, mutta kokonaiskuvaa ei ollut kenelläkään saatavilla yhdestä paikkaa”, selventää Tuominen.
Tuotannon ja kunnossapidon toiminnot reaaliajassa 3D Digital Twin -alustassa
Konecranes Smart Factory on älytehdasalustaan koottu palvelukokonaisuus, joka auttaa johtamaan tuotannon ja kunnossapidon päivittäistä toimintaa helposti ja tehokkaasti. Tuotannon näkökulmasta saadaan tärkeää tietoa koneiden pysähdyksistä ja niiden kestoista. Kokonaistehokkuuden kannalta on tärkeää pureutua suuriin tuotantokatkoihin ja niiden aiheuttajiin. Esimerkiksi näitä ovat laitteen toimintahäiriö, konerikko, asetusten määrittäminen, mittaukset, käyttäjäkunnossapito, materiaalin puute tai logistiikkaongelmat. Tavoite on päästä hyödyntämään datavirtaa tehokkaasti tuotantolaitoksessa, jossa päivittäistä tekemistä voidaan johtaa saatavan datan avulla.
Process Genius Oy:n toimitusjohtaja Jani Akkilan mukaan Konecranes ja Process Genius ovat tuoneet markkinoille digitalisuuden ja substanssin yhdistelmän, jota ei ole aiemmin toteutettu. Process Genius on systemaattisesti kehittänyt Digital Twin -alustaansa, jota Konecranes on substanssiosaajana kokemuksellaan rikastanut.
”Konecranes on tuonut alustan kehitykseen aidon ja viimeisimmän kokemuksen. Konecranes Smart Factory sovelluksessa yhdistyy tehokas kunnossapito ja tuotanto viimeisimpään 3D Digital Twin -alustaan”, Akkila kertoo.
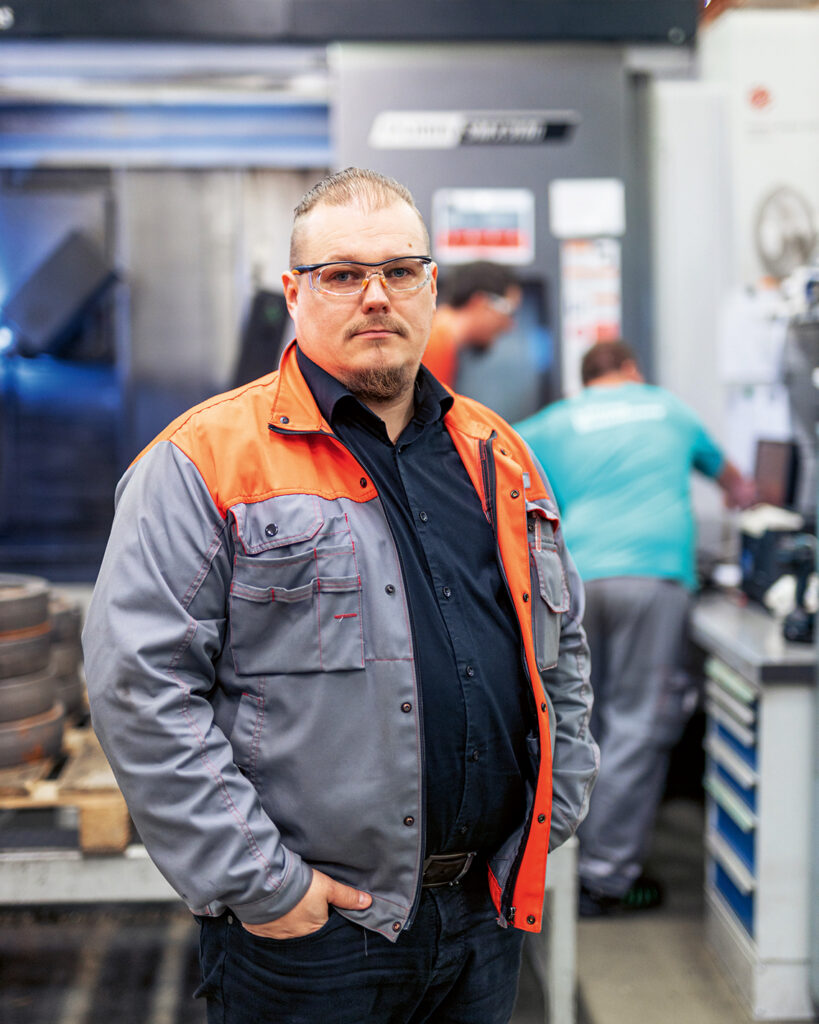
Tuottavuus on lisääntynyt puolen vuoden seurantajaksolla merkittävästi
”Ajantasainen tuotannon ja kunnossapidon tilannekuva on mahdollistanut Konecranesin Hyvinkään tehtaalla tuotannon johtamisen faktapohjaisesti. Sovelluksesta on saatu operatiivisessa käytössä hyviä tuloksia, ja tuottavuus on lisääntynyt puolen vuoden seurantajaksolla merkittävästi”, kertoo Konecranesin komponenttitehtaan tehdaspäällikkö Tuomas Patanen.
”Sovelluksen avulla on päästy kiinni myös hukkatunteihin. Käytännössä hukkatunteja kertyi esimerkiksi asetusajoista, odottamisista, pienistä hälytyksistä ja muista tuotantoa häiritsevistä seikoista. Nykyään päästään kiinni siihen, mistä hukkatunnit syntyvät ja pystymme mahdollisuuksien mukaan lyhentämään hukkajaksoja ja tekemään parannuksia prosesseihin”, selventää Patanen.
”Käyttöaste on koneilla noussut merkittävästi, sovelluksen avulla pystymme validoimaan, ovatko työn tekemiseen suunnitellut tunnit kohdallaan. Konecranes Smart Factory mahdollistaa paremman tehtaan monitoroinnin, ja saamme helposti selville mitä tehtaassa tapahtuu. Näin pystymme reagoimaan nopeammin esimerkiksi, siihen miksi kone on seisahtunut. Parasta on se, että sovellus on käytettävissä esimerkiksi puhelimessa, joka mahdollista etävalvonnan täysin eri tavalla kuin mihin on totuttu”, kertoo Tuomas Patanen.